Programm 2025
Erkenntnisse von Branchenexperten und Marktteilnehmern
4. Juni 2025 - Abendveranstaltung
Networking-Event mit feinem Essen, leckeren Getränken und Entertainment
Wir laden Sie herzlich ein, den Abend des 4. Juni 2025 mit uns in der REISERS Genussmanufaktur zu verbringen! Stimmen Sie sich schon hier auf die Veranstaltung ein! Kommen Sie miteinander ins Gespräch und tauschen Sie sich über aktuelle Themen der Zerspanungsbranche aus. Genießen Sie intensives Networking in stimmungsvoller Atmosphäre!
5. Juni 2025 - Fachtagung im Vogel Convention Center Würzburg
Check in & Welcome Coffee im Ausstellungsbereich
Eröffnung & Begrüßung, Vorstellung der Agenda und Ziele
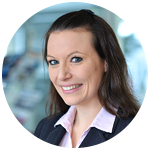
Frauke Finus
Leitende Redakteurin blechnet
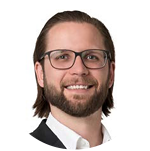
Benedikt Hofmann
Chefredakteur MM MaschinenMarkt
Schwerpunkt: Pressentechnik und Digitalisierung – im Doppel zum Erfolg
Smarte und autarke Systeme – Enabler für eine effiziente und optimale Produktion
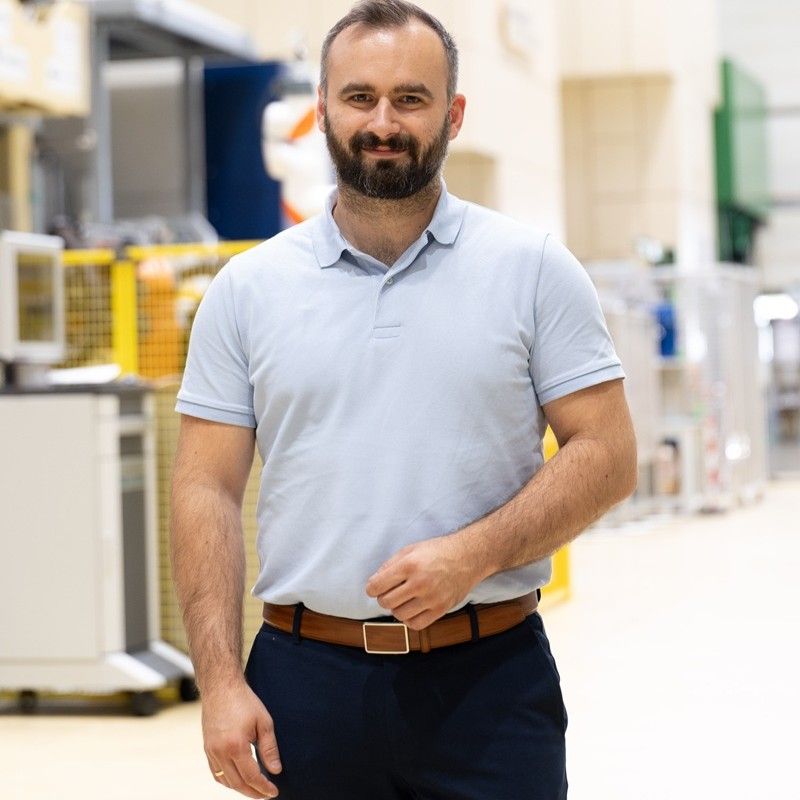
Fraunhofer IWU
Smarte Produktion – mit dem digitalen Prozess-Zwilling
AutoForm Engineering Deutschland GmbH
Effizienzsteigerung durch Laser Blanking - Wie digitale Lösungen dabei helfen, das volle Potenzial auszuschöpfen
Kaffeepause und Besuch der Fachausstellung
Innovation im Presswerk – Durch neue Technologien wettbewerbsfähig bleiben
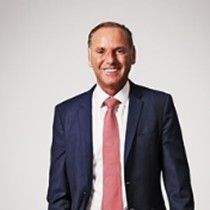
Fagor Arrasate Deutschland GmbH
Beautiful Data – Mehr Produktivität durch hochwertige Daten und kluge Auswertungen
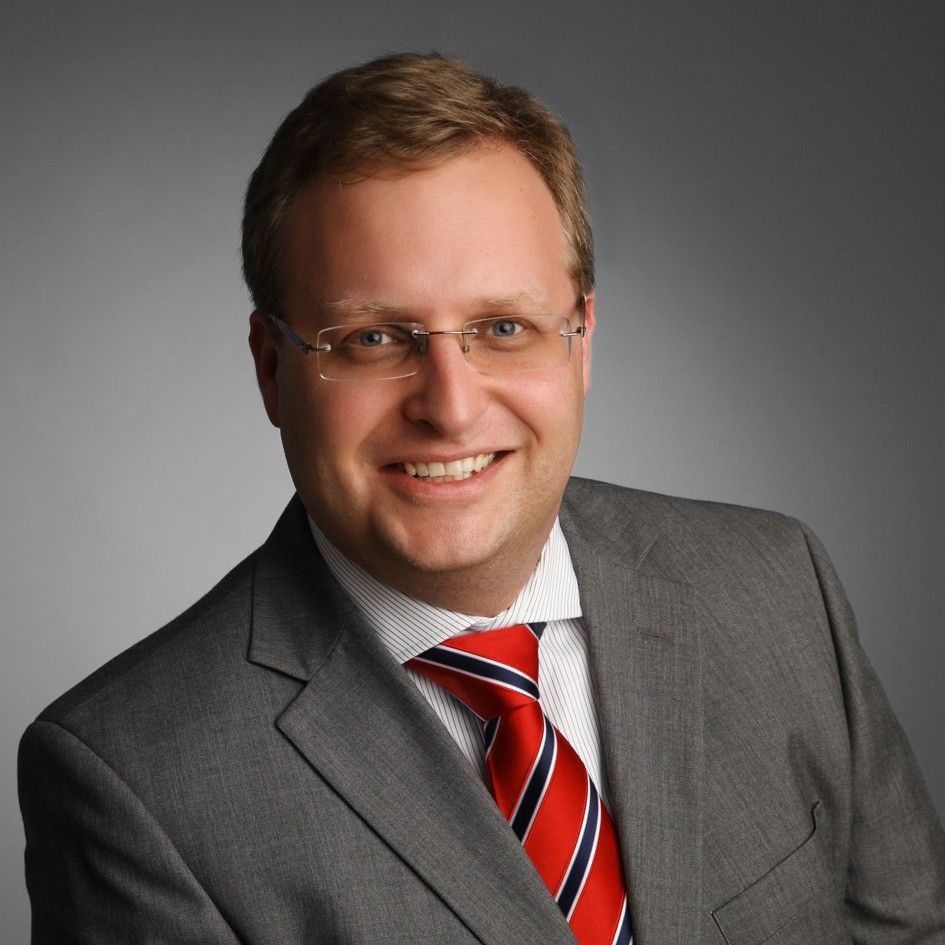
ConSenses GmbH
Effiziente und nachhaltige Produktion durch digitale Rückverfolgbarkeit in der Umformtechnik
Schwerpunkt: Jedes Teil ein Gutteil – Qualität als oberstes Gebot
Mehr Präzision im Presswerk: Zukunftsweisende optische Messtechnologien für höchste Qualitätsansprüche
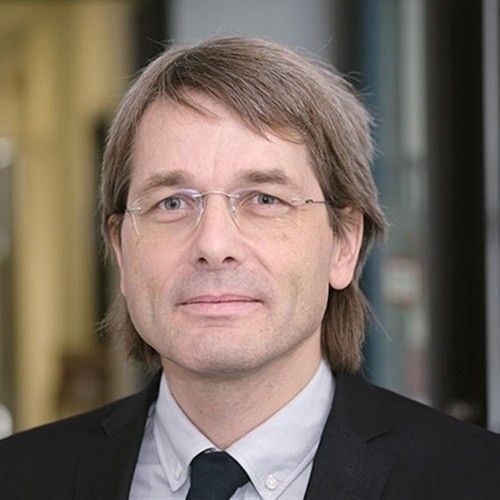
Fraunhofer IPM
Mittagspause und Besuch der Fachausstellung
Schwerpunkt: Dreh- und Angelpunkt Werkzeug
Einsatz von Verbundwerkstoffen als Gleit- und Führungselemente in Presswerkzeugen für die Kalt- und Warmumformung
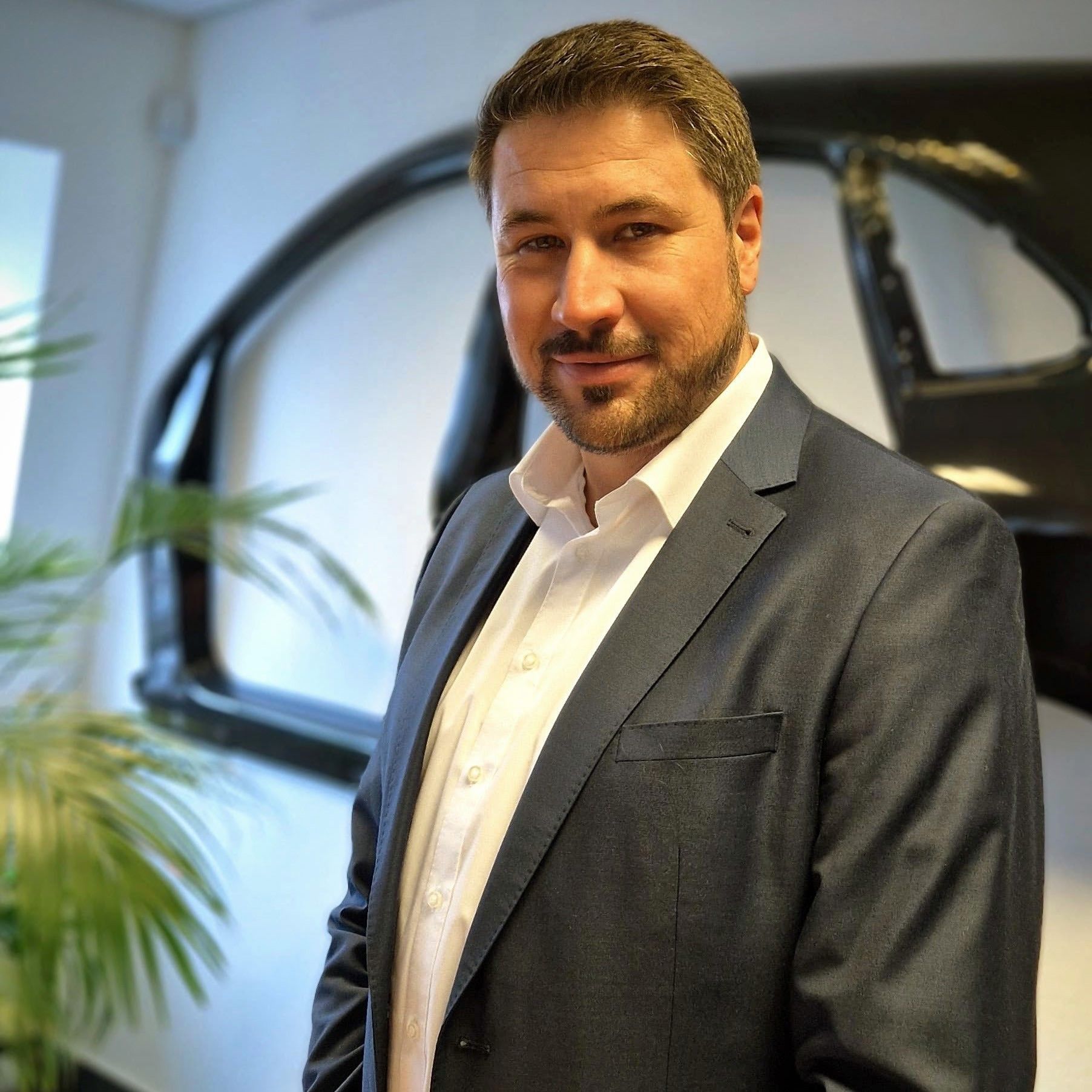
Dayton Progress GmbH
Pressencharakterisierung für die simulationsgestützte Bombierung von Karosseriewerkzeugen
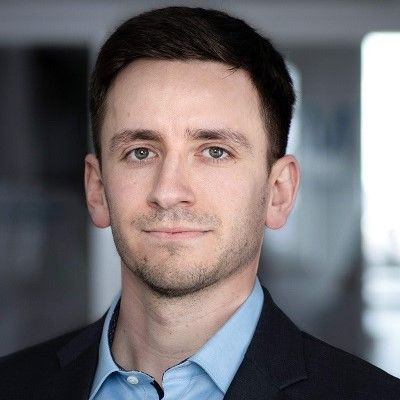
ICM - Institut Chemnitzer Maschinen- und Anlagenbau e.V.
Kaffeepause und Besuch der Fachausstellung
Schwerpunkt: Automation und Handling – Wenn es prozesssicher und schnell gehen muss
Verdeckte Potenziale in Presswerken entdecken durch Simulationen & Offline-Programmierung mit OpenLoop
Schwerpunkt: Gut geölt ist halb gewonnen
Innovative ölfreie Schmiermittelsysteme – Präzision und Nachhaltigkeit in der Metallumformung
Reduzierung von Ausschuss durch selektive und prozesssichere Nachbeölung der Platinen im Front of Line
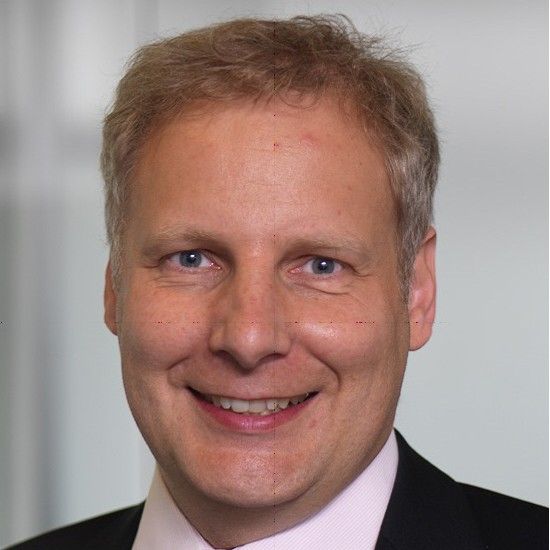
AMTEC Kistler GmbH
Closing Ideas und Get-together
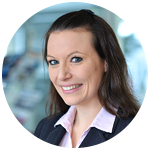
Frauke Finus
Leitende Redakteurin blechnet
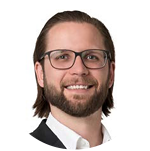
Benedikt Hofmann
Chefredakteur MM MaschinenMarkt